Pavimento de Gres Porcelánico: Características, desventajas, tipos e Instalación
Toda la información necesaria para tomar la mejor decisión de compra de Pavimentos Porcelánicos. Características, propiedades y desventajas, instalación, precio…
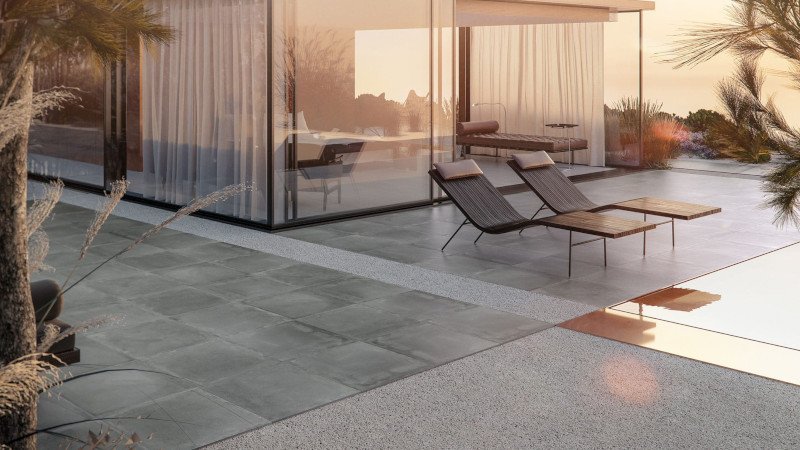
Desde hace unos años este tipo se suelo se ha hecho muy popular gracias a sus extraordinarias cualidades. Es muy resistente e increíblemente estable, muchos más que el gres tradicional, que ya de por sí es muy resistente. Por este motivo es ideal para zonas de alto tránsito como centros comerciales o edificios públicos, para las zonas más exigentes de una casa como la cocina o el baño, y especialmente como baldosa para exteriores.
La razón de ser de estas mejores prestaciones las encontramos en la utilización de una arcilla más fina, obtenida mediante procesos industriales, y un proceso de fabricación donde se utiliza más temperatura y presión. El resultado es un producto mucho más compacto, estable y menos poroso.
Además, las posibilidades de diseño que ofrece son muy amplias. Se puede encontrar no solo en diseños originales, también imitan otros materiales como la madera, los metales, el corcho o las tan de moda baldosas hidráulicas.
Por tanto, es lógico que el gres porcelánico se haya adentrado también en la viviendas. Cada vez es más habitual encontrar este tipo de suelos en los interiores.
Ventajas del Gres Porcelánico Respeto a otros Tipos de Gres
- Gran resistencia a la abrasión y golpes. Por tanto es ideal para zonas de alto tránsito y exteriores.
- Ofrece un mejor aislamiento cuando se usa como revestimiento de paredes.
- Muy estable dimensionalmente. Sus dilataciones y contracciones, incluso frente a cambios bruscos en la temperatura y condiciones ambientales, son limitadas. Alrededor de 0,5%.
- Muy baja absorción de humedad. Casi podemos decir que es completamente impermeable, más aún cuando está esmaltado.
- A diferencia de los otros tipos de gres es “no poroso”. Existe un riesgo mucho más bajo de que penetre cualquier producto y se manche.
- Mayor durabilidad. Olvídese de cambiar el suelo durante muchas décadas. Esto en parte ayuda a compensar su mayor coste.
- Prácticamente no necesita mantenimiento.
- Amplísima variedad de diseños. Los podemos encontrar en cualquier diseño. Porcelánicos imitación madera, mármoles, hidráulicos, etc. Pero también con diferentes texturas y con cantos con bisel o sin bisel.
Desventajas
- Precio sensiblemente superior. Hasta un 50% más. A lo que hay que añadir más tiempo de mano de obra.
- Instalación y manipulación más compleja.
- Son más densos, y por tanto también más pesados. Por lo que agravan este inconveniente de todos los tipos de gres, que es el de causar un estrés adicional a la edificación.
Tipos de Baldosas de Gres Porcelánicos
A la hora de hablar de diferentes tipos de porcelánicos nos vamos a fijar a si se le ha añadido una capa superficial, principalmente con criterios estéticos.
- Técnico o Compacto. Por definición todos los suelos porcelánicos son así, un compuesto homogéneo que es igual por todos los lados.
- Esmaltado. La diferencia radica en que se ha añadido un esmalte vitrificado con el fin de conseguir algún diseño concreto. Por ejemplo imitar madera, mármol u otro material.
El Precio de los Pavimentos Porcelánicos
La variabilidad en este caso es enorme. Se debe en gran medida a las diferencias de calidad, formato de la pieza, diseño y cache de la marca.
Para hacernos una idea el precio puede situarse desde los 20 €/m² hasta los 80 €/m². E incluso más en función de la exclusividad de la marca y/o el diseño.
Mantenimiento
Al ser un material no poroso el mantenimiento es realmente reducido. Salvo algunos tipos de ácidos, los líquidos no penetraran, así que olvídate de las manchas. Con un simple trapo húmedo podremos eliminar cualquier líquido que se haya derramado.
Para la suciedad bastará con barrer o pasar la aspiradora. Y periódicamente pasar una fregona con algún detergente de pH neutro para desinfectar.
Fabricación y Composición
Los suelos porcelánicos difieren en su proceso de fabricación respecto a otros tipos de pavimentos cerámicos. Las arcillas extraídas y seleccionadas son atomizadas, es decir, convertidas en polvo. Luego se cuecen a altas temperaturas, superiores a los 1.100 grados, durante un periodo de entre 25 y 30 minutos. Luego se deja enfriar a temperatura ambiente.
En algunas ocasiones también se producen baldosas porcelánicas a través de un proceso de extrusión (en el cual la mezcla no está seca sino en formato de pasta) para que puedan ser troqueladas. Esto permite obtener una gran variedad de formatos.
Es habitual, que en las piezas no esmaltadas se pula la superficie para dar cierto brillo a la pieza.
Acabados
Las baldosas a las que no se les aplica ningún tratamiento superficial durante la fabricación, o posteriormente, tienen un aspecto rugoso y mate.
En algunas ocasiones se le añaden sales antes de la cocción. Esto da un acabado satinado y una superficie más fácil de limpiar.
Sí además, tras la fabricación se pule mediante procesos mecánicos, se obtienen piezas con brillo. El inconveniente en este caso es que se debilita la resistencia frente a las manchas, por lo que no se aconseja su uso en exteriores.
Tamaños y Formatos Habituales
Una de las grandes ventajas de este material son las posibilidades de fabricación. Se puede conseguir casi cualquier formato y tamaño. Desde unos pocos centímetros a piezas enormes.
Mientras que lo más habitual son los formatos cuadrados y rectangulares, nos encontramos con que los formatos hexagonales de suelos porcelánicos están muy de moda últimamente. Vemos como muchas revistas de decoración los incluyen y suponemos que los próximos años serán muchos más habituales en los catálogos de fabricantes y distribuidores.
En cuanto a tamaños lo más frecuente es:
- 30x60 cm
- 60x60 cm
- 80x80 cm
Llama la atención como el tamaño de 30x30, el más habitual entre los otros tipos de gres, no es tan demandado en porcelánicos.
Respecto a los espesores lo normal es que se sitúe entre 0,8-1 cm. Sin embargo se pueden encontrar porcelánicos ultrafinos de hasta 3 mm. Aunque en este último caso su uso estará más enfocado a revestimiento de fachadas.
Principales Empresas Fabricantes y Marcas de Porcelánicos
Existen muchos fabricantes y marcas de suelos porcelánicos.
- Porcelanosa.
- Levantina.
- Vives.
¿Cómo distinguir un porcelánico de otros tipos de gres o cerámica?
Si no tenemos a mano la caja o embalaje existen varias formas de distinguir un porcelánico. Ninguna es un método 100% efectivo, aunque si nos valdrá en la mayoría de ocasiones.
Lo más habitual es que tanto el gres rústico, como el esmaltado o un suelo de cerámica tradicional están fabricados con pasta roja o blanca. Es decir, si le damos la vuelta veremos este color. Un porcelánico no tiene porqué ser así. Si vemos que se sale de esta gama de colores es muy probable que sea porcelánico. Hay que tener en cuenta también que hoy en día también muchos porcelánicos son también esmaltados.
Otro método es tratar de rayar la parte trasera. En los porcelánicos conseguir marcarlos requiere de mucha fuerza.
Y por último la técnica de la absorción de agua. Como hemos dicho es el gres porcelánico es muy poco poroso. Si dejamos caer una gota de agua esta no será absorbida por el material. Por el contrario, si no lo es, veremos cómo algo de agua penetra en la pieza de gres. De los tres métodos, este debería ser el más fiable.
Instalación de Suelos Porcelánicos
La instalación de cualquier suelo es algo fundamental. En el caso del gres una mala instalación implica un mal suelo, independientemente de la calidad de la baldosa y de lo que nos haya costado.
Es imprescindible mano de obra de calidad y materiales de calidad. Dicho esto, mi recomendación es que la instalación de suelos porcelánicas no es apta para aficionados a la reformas y el bricolaje.
Recomendaciones:
- Respecto al mortero a utilizar se recomienda para un agarre perfecto el cemento cola porcelánica, tipo C2.
- Colocación utilizando doble encolado. Es decir, se pone el mortero tanto en la pieza como en el soporte con el fin de mejorar la adherencia.
- Intercalar piezas de diferentes cajas. El motivo es mejorar la uniformidad del conjunto del suelo. Pueden existir pequeñas diferencias si unas piezas se han fabricado en diferentes momentos del tiempo, y colocando juntas todas las de una misma tanda la diferencia con el resto puede ser significativa.
Las Juntas de Colocación
Hay que tener en cuenta que todos los materiales, sin excepción, alteran su volumen frente a cambios de temperatura, humedad, etc. En algunos casos estos cambios son significativos que otros.
En el caso que nos ocupa, los pavimentos porcelánicos, este índice es mucho menor, como ya hemos señalado, pero aun así hay que considerarlo. Además, no será el único material presente en una instalación.
Las juntas de dilatación son el espacio que se deja entre baldosas con el fin de absorber estos pequeños movimientos. En esta ocasión entre 2 y 3 milímetros es lo habitual. Aunque siempre habrá que consultar las recomendaciones del fabricante.